The steel market just shifted. If you’re running a shop that bends, cuts, or welds anything structural, this deal affects you. Here’s what to watch, and what to do next.
The Deal: A $15 Billion Buy and $11 Billion in Upgrades
Nippon Steel’s $14.9 billion acquisition of U.S. Steel comes with major implications for the North American manufacturing landscape. The company has committed $11 billion in upgrades across U.S. Steel’s blast furnaces and electric arc operations. These investments are likely to lead to changes in the types of steel being produced, with new materials, improved tolerances, and higher consistency.
For most fabricators, this won’t require new hardware. But it will challenge how quickly teams can update weld specs, qualify new processes, or adapt to shifts in part performance.
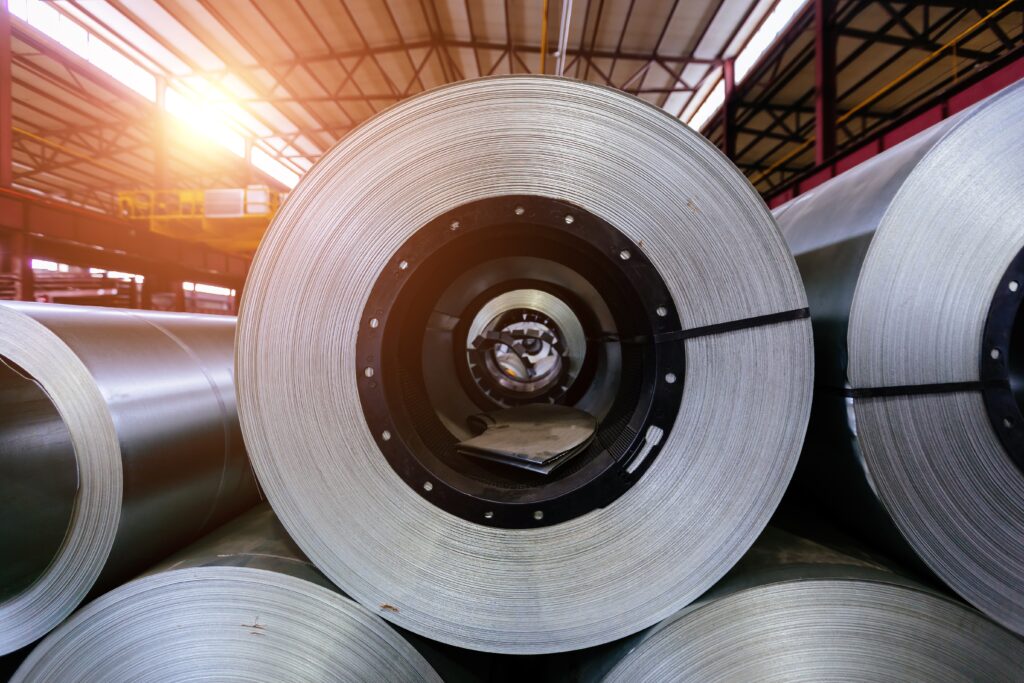
Engineering Will Adapt First. Your System Should Keep Up
Changes in material grades or sourcing will show up first at the engineering and process level. Welding automation systems don’t need to be replaced every time the steel spec changes, but they do need to adapt.
Whether your system is built from a single platform or integrated from multiple sources, what matters most is how easily your team can update parameters, qualify new welds, and keep moving without disruption.
If your robot, power source, and controls support flexible programming and fast recovery, your team stays productive when others are waiting on rework or external support.
The Golden Share: Why This Is Not Just a Business Deal
Part of the acquisition included a “golden share” arrangement with the U.S. government. That means federal authorities have veto power over decisions like plant closures, asset transfers, or strategic shifts. This political oversight introduces long-term unpredictability in where and how domestic steel is produced.
For manufacturers, this means agility matters more than ever. Shops that can pivot quickly by adjusting weld settings, qualifying new parts, or scaling up a second shift will outperform those that can’t.
Why This Matters to Job Shops and Mid-Sized OEMs
As U.S. Steel modernizes and possibly shifts product lines, large manufacturers may pass changes downstream. That puts pressure on job shops and smaller OEMs to adapt faster than ever. These shops can’t afford systems that require outside contractors to change a weld path or troubleshoot inconsistent results.
Welding automation is no longer just a cost play. It’s how smaller operations stay competitive when part mix increases and lead times shrink.
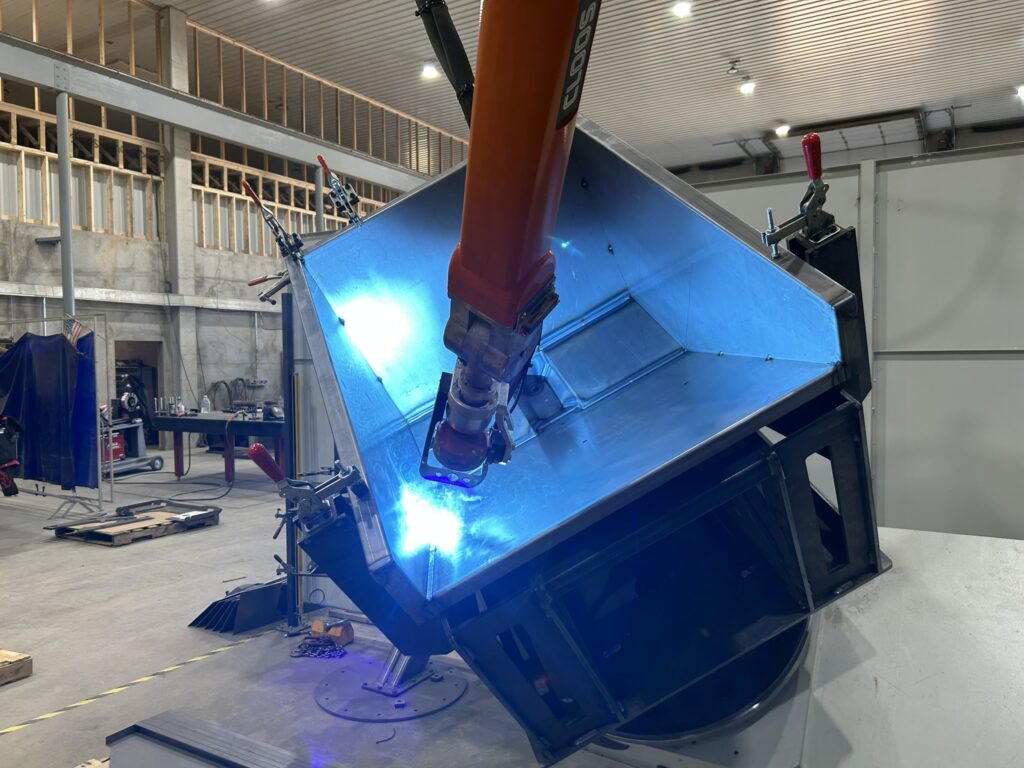
What You Can Do Right Now
- Evaluate your parts Are any of your weld procedures tied to specific material properties? Would a shift in grade or source affect your bead profile or joint prep?
- Review system flexibility Can your welding cell accept new procedures easily? Are parameters locked behind service calls or integrator-only access?
- Get ahead of downtime If plant upgrades impact steel availability, your system needs to be running, not waiting on support or part replacements.
Final Thought: Being Ready Is the New Advantage
When supply chains shift, the winners are the teams that adapt faster. Welding automation doesn’t have to change every time steel specs do, but your ability to reprogram, qualify, and move with confidence is where the payoff lives.
That’s where well-integrated, weld-ready automation proves its value. It helps your team respond to changes without grinding production to a halt.
Things are shifting fast in the steel world. If you’re not sure how that affects your welds, your parts, or your timelines, let’s talk it through.