How Link-Belt Cranes is Doing Automation Right
- Home
- Resources
- Case Studies
- Link-Belt Cranes

COMPLEX JOBS CALL FOR UNCOMPLICATED SERVICE.
As a global leader in telescopic and lattice boom cranes, Link-Belt Cranes designs equipment that performs under pressure, lifting immense loads with precision and reliability. When the team set out to automate their production, the expectations were high and the tolerance for error was low. They needed more than a vendor. They needed a partner who understood the demands of structural welding and could deliver a solution that worked from the ground up. That’s why they chose CLOOS.
“We know you can pick up the parts and move them. But do you understand the right way to weld them?”
— Manufacturing Engineer, Link-Belt Cranes
THE PUNCHLIST
The Customer: Link-Belt Cranes, Lexington KY
The Need: To weld long structural components requiring multiple high-deposition passes—work traditionally done by skilled operators who were becoming increasingly hard to find amid rising production demands.
The Fix: CLOOS delivered a blend of custom-engineered and pre-configured welding systems tailored to Link-Belt’s exact workflow. Systems integrate automation for positioning, fixturing, and deposition—built for longevity, precision, and ease of use:
-Six total systems: five custom, one pre-configured
-Tackled long, multi-pass weldments
-Reduced downtime through a direct OEM service model
-Minimized retraining time via intuitive control systems
-Delivered a high-quality weld finish with less operator fatigue
The Bottom Line: Repeatable quality. Easier troubleshooting. One partner for design, support, and service.
THE CHALLENGE
Link-Belt wasn’t new to automation. But their applications required a specific type of expertise—welding knowledge first, robotics second.
During their vendor search, many companies could offer robots. Few understood the weld. The question was never “can this weld be automated?” It was “can it be automated the right way?”
“[CLOOS] was the welding source, they were the integrator. They were who you call when you break down. It was everything.”
-Link-Belt Cranes
THE SOLUTION
CLOOS took the time to listen—not just to specs, but to the weld sequence, the material behavior, and the impact on production. From there, they developed:
– Welding systems capable of handling thick-gauge materials and long parts
– Control schemes aligned with Link-Belt’s weld procedures
– Integrated service, training, and part support from a single partner
– A system architecture that’s scalable and serviceable without redesign
Increased Productivity:
Engineered to reduce operator fatigue and meet production targets.
Improved Efficiency:
Custom systems tailored to Link-Belt’s specific parts sequences.
Stronger Partnership:
All hardware and controls designed by CLOOS- no finger-pointing when service is needed
Let’s Talk Shop
Get in touch with one of our product specialists. We’ll walk you through the options, answer your questions straight, and help you choose the welding automation that fits your shop – and your goals.
YOU MAY BE INTERESTED...

Construction and Heavy Equipment
CLOOS delivers scalable welding automation solutions for construction and heavy equipment manufacturers. Whether you’re building loaders, cranes, or dump trucks,

Articles
Explore expert insights and actionable tips on digital marketing, branding, and online business growth. Stay updated with CLOOSNA’s latest articles
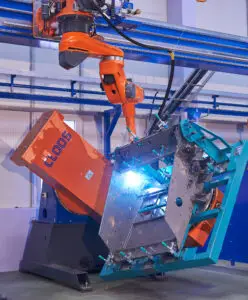
Products
Explore our comprehensive lineup of welding solutions, including plug-and-play cells and custom-designed full-scale lines, all crafted to deliver precision and